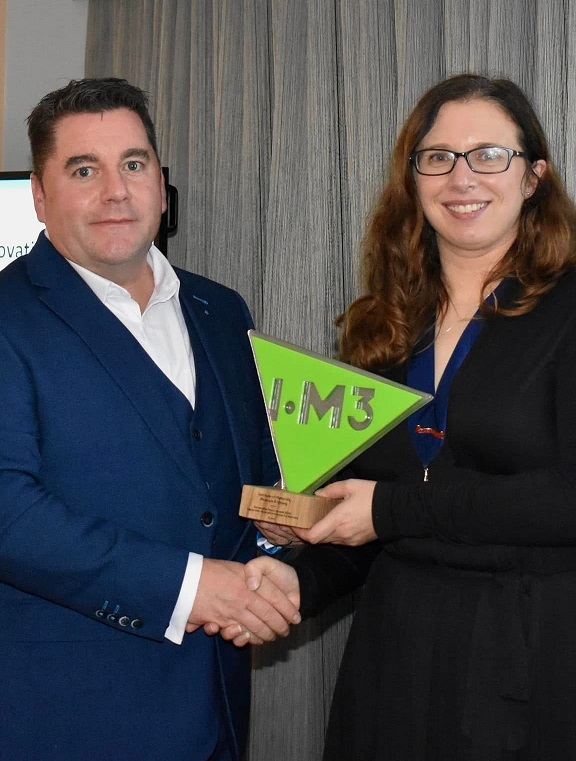
A Tameside company is revolutionising the production of conveyor belts to make them more sustainable.
Conveyor belts are the workhorse of the modern economy involved in every part of the manufacturing and distribution process. Most consumers are totally unaware of the key role that conveyor belts play in supplying the goods they buy every day but without them the global economy would grind to a halt. Everything we buy from pillows to pasta will have been carried on a conveyor belt. The fulfilment centres that process online shopping orders have miles and miles of conveyor belts. Supermarkets, gyms, airports and even ATMs all make use of conveyor belts.
The widespread use of conveyor belts means that when they break most of them end up going to landfill or are incinerated at considerable cost to the environment. With many manufacturers preferring to fit new conveyor belts rather than make repairs, 80% of belts fail prematurely at the joint due to it being only 1/3rd the strength of the belt.
Ecobelt uses a revolutionary new Belt Splice Technology called AnnStuMax™, which is up to five times stronger than the belt itself, therefore eliminating the historical weak link. It will dramatically transform the belting world and improve the Ecotoxical implications of belt use on the planet whilst delivering significant financial savings for clients.
Craig Spencer-Smith invented AnnStuMax™ in 2017 whilst trying to develop a belt splice as strong as the belt itself.
“Many consumers are very concerned about their impact on the environment,” Craig says. “But they don’t realise the role conveyor belts play and the amount of waste that they create. If it’s been made, it’s been conveyed. Our aim is saving the planet, one belt at a time.”
The manufacturing process of the materials used in conveyor belts, and the production of belts consumes huge natural resources while producing significant greenhouse gases throughout all the stages of the products life. Longer in use, repair and reuse will minimise materials use and waste, practise complete traceability and use new re-manufacturing services.
Ecobelt also provides a consultancy service which advises clients on reducing their conveyor belt usage. The service offers a scientifically accurate Ecotoxical footprint of the belts on-site. They provide advice on prolonging the use of belts for significant cost savings, using less energy and reducing water consumption during cleaning.
AnnStuMax™ has been independently tested and analysed by the Sustainable Materials Innovative Hub of the Henry Royce Institute at the University of Manchester. Ecobelt has also conducted over 50 successful real-world trials with both Greater Manchester Mayor, Andy Burnham, and Jonathan Reynolds, Secretary of State for Business and Trade, taking part in the ‘Hall of Fail’ tests, which sees invitees trying to smash through the AnnStuMax™ joint with a bolt and lump hammer. To date nobody has!
Ecobelt recently won the Sustainable Materials Innovation for Net-zero category for the IOM3 Sustainable Future Awards 2024 (pictured). They have now been shortlisted for Collaborate to Innovate award and have been nominated for the Earthshot 2025 prize.
Ecobelt have taken an active part in the National Material Innovation Strategy [NMIS] and are being used as a case study in this important national document which will help shape government policy in this area. They will be present at the handover to government in early 2025 at the Palace of Westminster.
For more information on this groundbreaking technology, you can contact them through their website, where they will be happy to explain the positive implications of AnnStuMaxÔ - Saving the planet, One belt at a time.
For more information about Ecobelt, click here.